Some Comparisons with Other Approaches
SCARA robots for precision assembly
Probably most of the precision assembly lines in the world use the highly successful SCARA robot invented by Makino in Japan in 1972. Often, rows of SCARAs are linked by motorized conveyances. The robot must have a large workspace to access one or more parts feeders and must have very high accelerations and speeds for reasonable cycle times. Very often, the mass of the SCARA is hundreds of times larger than the masses of the parts it is carrying. Conveyors tend to have limited flexibility, have difficulty turning corners, lack motion precision, and generate debris. |
![]() |
The situation can be somewhat improved by parts kitting, where the sub-assembly and its parts are carried along the conveyor on pallets. Unfortunately, this requires one or more upstream kitting operations, and a number of expensive pallets. It has been shown that kitting per se does not add value to the product being assembled. | ![]() |
A well-known modular assembly system uses SCARAs equipped with grippers on a six-position turret to handle up to five different parts and also move pallets into and out of its workspace. In this system, both products and parts must flow through the factory. All parts are held in parts-specific trays which are loaded in upstream vibratory parts feeding stations. This solution takes up a lot of floor space, is not very easy to reconfigure and requires the potentially complicated turret gripper mechanisms. | ![]() |
Some comparisons between SCARA and minifactory
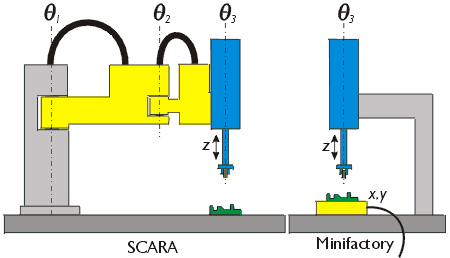
The SCARA robot executes 4-DOF assembly using its shoulder and elbow joints to access a point in the plane, and its roll and vertical translation joints to bring a part to its correct position and orientation in the product sub-assembly. This arrangement gives the SCARA a large workspace, but also requires it to have large and powerful actuators, even though the parts handled are generally small. The shoulder and elbow joints are highly problematic for precise motion in the plane, since the joint angle encoders are located far from the end effector, and there are intervening friction and dynamic effects. In minifactory, the product courier replaces the shoulder and elbow joints of the SCARA, and the roll and vertical translation axes are fixed in space. Because encoders and actuators for all axes in minifactory are co-located, intrinsic precision in minifactory can exceed the typical SCARA's by two orders of magnitude. Additionally, minifactory uses about an order of magnitude less floor space to assemble the same size product, and eliminates the need for conveyors. In minifactory, each roll/translation module handles a single part type fed by a local parts feeder.
Planar motors for precision assembly
Planar motors are already in use in several different commercial precision assembly systems, and already offer certain advantages over SCARA-based systems. Typically, multiple planar motors hanging from a platen ceiling perform pick and place operations on a sub-assembly. In this respect, operation is similar to a SCARA, although precision generally exceeds that of a SCARA. There are, however, several limitations. All the work must take place essentially within the sandwich formed by the platen and base planes. Thus, the height of all the robots is fixed, making it necessary to have long z axes in order to access parts and all heights of a sub-assembly. The moving part of each axis, however, must be less than half the total z length. Long z axes reduce precision. An important restriction is that only a limited number of robots can operate on a given platen. Some arrangements link multiple planar motor systems together via conveyors. In these cases, the assembly line resembles a SCARA assembly line. Finally, planar motors in commercial use operate on an open-loop stepping principle. They operate at lower peak accelerations and velocities than is possible in order to avoid missing steps, have poor disturbance rejection, and use power even when not moving.
Some comparisons between planar motor systems and minifactory
In contrast with commercial planar motor systems, the minifactory platens face upwards and are field joinable to form platen ensembles or highways. In minifactory, the couriers are based on novel closed-loop planar motors rather than open-loop steppers. They operate at high efficiency, can't lose steps, and reject disturbances. In commercial systems, the planar motors carry additional translational and rotational axes. In minifactory, they carry product sub-assemblies and participate with manipulators and overhead processors to do assembly operations. In minifactory, the vertical height of manipulators and overhead processors is unrestricted. Additionally, each manipulator and overhead processor is individually adjustable in height, whereas in commercial planar motor systems, all robots are at the height defined by the platen. In commercial planar motor systems, a central computer controls up to four or even six robots. In minifactory, each robotic agent (e.g. courier, manipulator, overhead processor) has its own computer.
Summary
In the table below, we have tried to summarize some of the main differences between today's practice and our goals for AAA/minifactory.
SCARA Systems | Planar Motor Systems | AAA/Minifactory Goals | |
---|---|---|---|
Design, deployment, programming time | 3-5 months | 2 months | 1 week |
Floor Space | large room | small room | tabletop |
Precision | 50 - 100 microns | 2-10 microns | 1 micron or below |
Typical robots | 4-DOF SCARAs | 4-DOF modules | 2-DOF modules |
Execution control | centralized | centralized | distributed |
Computers | few | few | many |
Product flow | conveyor belts | conveyors or none | planar robots |
Integration of fastening technologies | difficult | difficult | easy |
Parts feeding | kitting, conventional, flow-through | kitting, conventional | localized |